DISCOVER DRIVING THAT’S SMARTER, SAFER, EASIER, AND MORE EXCITING.
NISSAN INTELLIGENT MOBILITYINNOVATION AND EXCITEMENT LIVE HERE EXPERIENCE NISSAN
NISSAN INTELLIGENT MOBILITY
YOUR RESPONSIVE PARTNER
NISSAN INTELLIGENT MOBILITY
A BOLDER RIDE THROUGH LIFE
When drivers, their cars, and their communities are in sync, our world becomes a better place. Discover driving that’s smarter, safer, easier, and absolutely thrilling.
Quality
From conception to car construction, from testing to transparency, from customer service to commitment. Quality is in every fine detail.
SHOWTIME ALL THE TIME
It’s at glamorous international motor shows that Nissan unveils its latest models and exciting concept cars such as the Nissan Sway concept and Lannia concept car. Read on to find out all the latest show news from around the world.
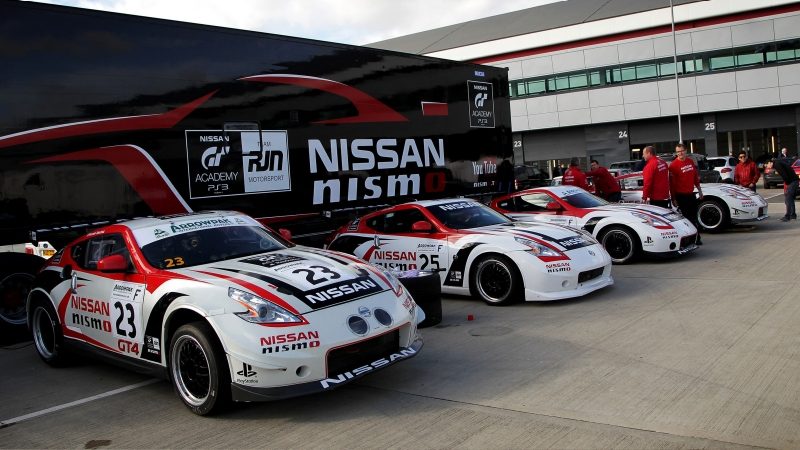
THE ULTIMATE TEST
We head to the racetrack not just for the adrenalin. Motorsport is the ultimate proving ground for the innovations in your Nissan, and has led directly to the creation of our race-bred high-performance NISMO models.
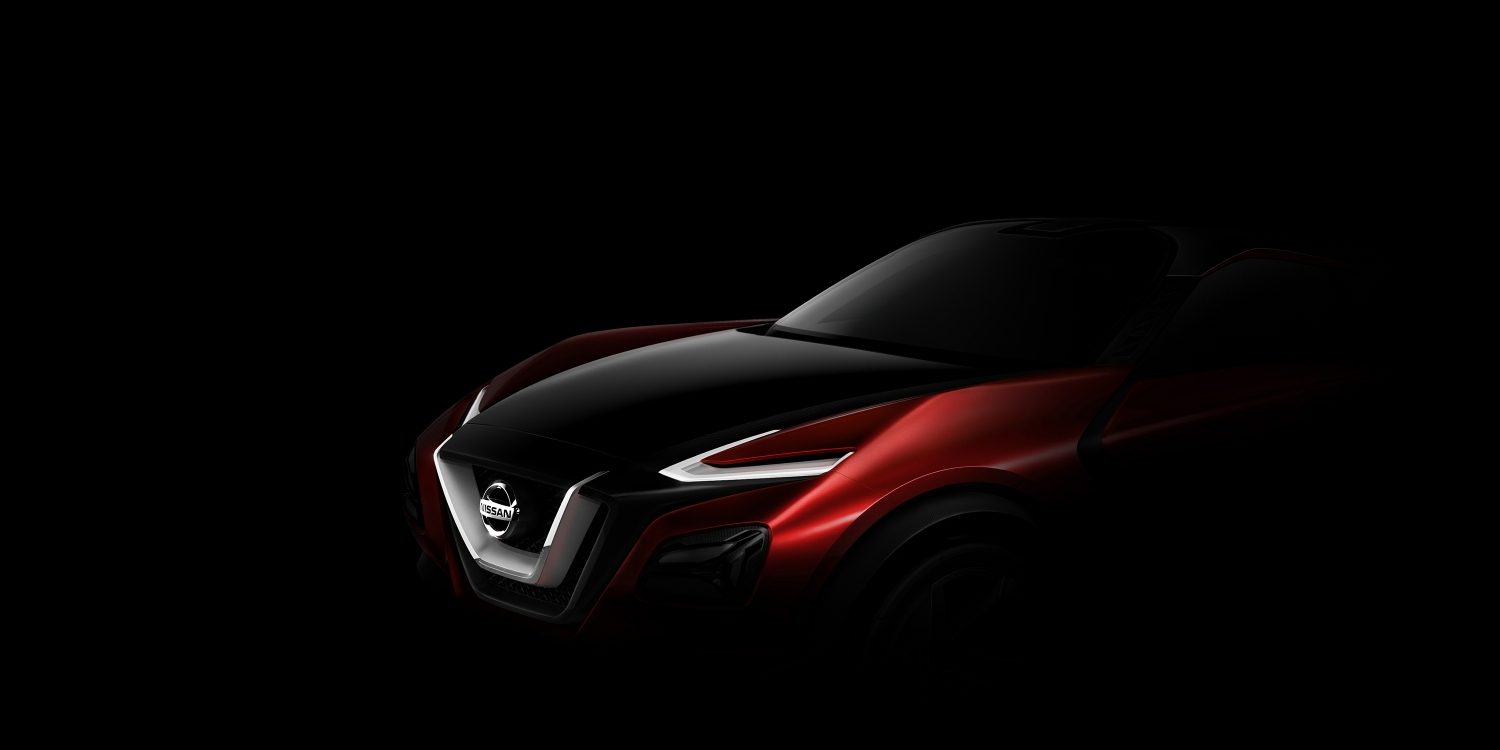
A look into the future
Concept cars
Inspired by a vision of safer, more sustainable, and exciting mobility.
Concept cars